Research & Study
Countrywide Tannery Mapping in Bangladesh
December, 2021
The leather sector of Bangladesh, which constitutes about 3 percent of the world’s market for leather and leather goods, is the country’s third-largest source of export earnings, after readymade garments and jute and jute products. The tanneries are located in five districts of Bangladesh. They are Dhaka, Gazipur, Jessore, Khulna, and Chattogram. As of December 2021, 135 tanneries are in operation in TIE. Earlier these tanneries were in Hazaribagh, Dhaka, which was relocated to Hemayetpur. In terms of labour standards and workplace safety, the leather tanning industry is no exception from the countrys other labour-intensive industries, where sweatshop conditions are commonplace. Even after the relocation that promised better lives and work conditions for the tannery workers, the industry is still struggling to ensure the minimum wage, basic labour rights, and occupational safety and health. Thus, the leather tanning industry in Bangladesh, failing to successfully deal with the challenges of weak environmental compliance on the one hand and poor labour standards and occupational safety on the other, has become subject to underperformance.
Background
Hazaribagh was the home of over 90 percent of tannery factories with an estimated land size of just 70 acres. The government of Bangladesh relocated the tannery factories from Hazaribagh to a newly developed tannery estate in Savar, a suburb of the Dhaka district. The new site was planned to be equipped with the facilities of a Central Effluent Treatment Plant (CETP), a central dumping yard, a water treatment plant, a Sludge Power Generation System (SPGS), and a Common Chrome Recovery Unit (CCRU), and a sewage treatment plant. Since 2012, the tanneries have slowly begun to relocate to the Savar tannery estate. Despite the high promise of a planned relocation project, the tannery estate in Savar has yet to achieve the major relocation objectives, e.g., environmental compliance, due to, among others, the CETP — the centerpiece of the whole relocation endeavor proving unsuitable for the tanning factories. As a result, without a functional CETP, all the factories are operating by polluting the environment.
Objectives
- To explore tannery industry across the country, assess the working conditions in tanneries and leather industries in Savar and Hazaribagh after the relocation has happened.
- To assess the socioeconomic aspects of tannery workers (i.e., age, gender, sex, education, disability status, living conditions, water and sanitation, and health).
- To assess the local tanneries' supply chain linkages and recent export performance and the prevalence of child and female labour in tanneries.
Findings
- Most of the workers in the tanning industry belong to the age group between 18 to 35 years and from five districts: Noakhali, Barisal, Dhaka, Chandpur, and Rangpur.
- 9.1% had a formal contract whereas, among the workers of un-unionized tanneries, 3.4 percent had a formal contract. 96% of the workers joined the sector without any training.
- One-third of the workers report that there is a separate latrine facility for male and female workers in the tannery. Fire safety is very poor.
- The average monthly earning of the workers in unionized tanneries is BDT 14223, which is BDT 13945 in the un-unionized tanneries. A female worker in the unionized tanneries earns, on average, BDT 12721 per month whereas a female worker in the un-unionized tanneries earns BDT 10421
- 53% are dissatisfied with their job and about half of the daily/temporary workers have shown their dissatisfaction.
Recommendation
- Employers must respect the rights of workers. They must provide a safe and healthy workplace for the workers. In addition, employers need to train new workers if the job involves working with toxic chemicals or other materials such as machinery that might potentially cause workplace hazards.
- Employment in the tannery factories must be formalized by requiring the employers to offer the workers a written and signed contract citing the duties and responsibilities as well as compensation and employee benefits. Formalization of employment is central to eliminating the current sweatshop conditions and ensuring decent pay with improved labour standards in the tannery industry.
- Workers need to be aware of their rights and protest incidents of labour violations through legitimate collective actions, i.e., union activism. They must exercise democratic practices in union organizing, which are critical to the effective functioning of trade unions on the one hand and preventing the politicization of union activism on the other. Large-scale campaigns and awareness-building programs may be arranged with the involvement of international labour rights and union organizations to foster union democracy.
The recent relocation of the tanneries from Hazaribagh to Tannery Industrial Estate at Savar has brought major changes in the lives of the workers. Some of the workers have to shift entirely to Savar with their families, some of them have to leave their families at Hazaribagh, and some of them have switched their jobs. The lack of educational institutions, health institutions, and required services near to their work has increased the level of dissatisfaction among the workers. More importantly, about 63 percent of the workers have shown their concern about low wages in this sector. The study shows that the workers do not get the minimum wage as supposed to be paid according to the Government Gazette. Though the unionized tanneries maintain the 48-hour conditions of international labour standards but the majority of the workers of un-unionized tanneries do not comply with the condition. Most of the workers have to work over 8 hours a day and over 48 hours a week. Therefore, nearly 10 percent of the workers have mentioned that long working hour is a major problem in their tanneries.
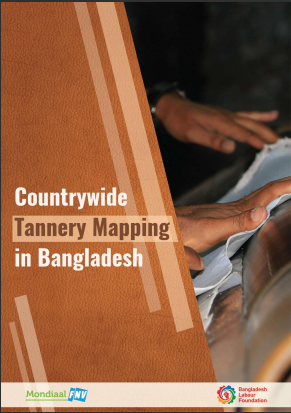
Publication Details
Date: December, 2021
Contact
Bangladesh Labour Foundation (BLF)
107 Bir Uttam C.R. Datta Road
Dhaka – 1205
Bangladesh